-
Steel Rail Wheels
-
Railway Wheel Set
-
Train Rail Wheels
-
Aluminum Alloy Wheels
-
Railway Spare Parts
-
Elastic Rail Clip
-
Railway Vehicles
-
Rail Wheel Axle
-
Steel Track Rail
-
Railway Fish Plates
-
Railway Tyres
-
Precision Forging Parts
-
Investment Casting Parts
-
Railway Track Fasteners
-
Railroad Track Cars
-
Rail Track Measuring Equipment
Q235 Q345 Steel Railroad Track Tie Plates Hot Forging Casting OEM
Place of Origin | China |
---|---|
Brand Name | Kingrail |
Certification | CE ISO CCC ROHS |
Model Number | 115 RE |
Minimum Order Quantity | Negotiable |
Price | Negotiable |
Packaging Details | standard export package, or as per customer request |
Delivery Time | 1-30 working days |
Payment Terms | L/C, D/A, D/P, T/T, Western Union, MoneyGram |
Supply Ability | 10000 ton/year |
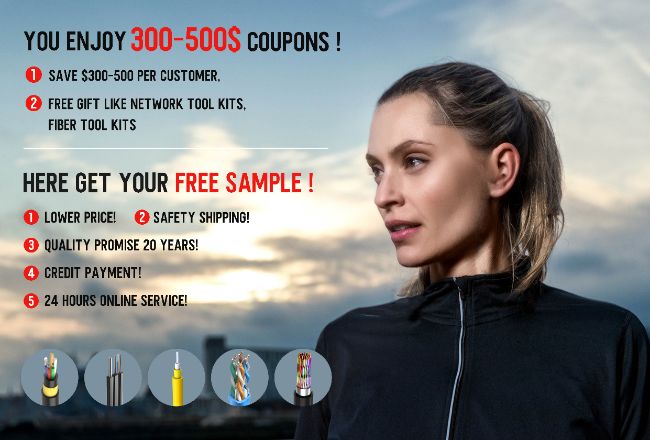
Contact me for free samples and coupons.
WhatsApp:0086 18588475571
wechat: 0086 18588475571
skype: sales10@aixton.com
If you have any concern, we provide 24-hour online help.
xMaterial | Q235 Or Q345 Steel | Production | Casting Or Forging, Hot/cold Rolled |
---|---|---|---|
Standard | BS, DIN, GB, JIS, UIC, Etc | Processing Service | Moulding, Cutting |
Application | Rail Construction Project Maintenace | Quality Control | Semi-finished Inspection And Finished Inspection |
Highlight | Q345 Steel Railroad Track Tie Plates,Q235 Railroad Track Tie Plates,OEM Railroad Tie Plates |
Introduction of Q235 Q345 Steel Railroad Track Tie Plates Hot Forging Casting OEM
A tie plate, baseplate or sole plate is a steel plate used on rail tracks between flanged T rail and the crossties. The tie plate increases bearing area and holds the rail to correct gauge. They are fastened to wooden ties by means of spikes or bolts through holes in the plate.
Material: Steel, Q235, Q345
Surface:Zinc Plated,Hot Dip Galvanized,Plain,Painted Coating, black
Process: Drop forged,casting
Color: Self Color,silver or others
Some specification of casting material as below:
1. Production for Q235 Q345 Steel Railroad Track Tie Plates Hot Forging Casting OEM
The railway cast iron backing plate is produced by the lost foam method, and is smelted in a 60kg intermediate frequency electric furnace. During the pouring process, the vacuum degree is maintained at 0.03 MPa, and the pouring temperature is 1580°C. Its chemical composition w is: 0.46%C, 0.23%Si, 0.59%Mn, 0.015%S, 0.024%P. After the casting is boxed, it is shot blasted and then annealed. The heat treatment process is: heating temperature 850℃; holding time 2h, cooling to room temperature with the furnace (total 12h).
2. Organizational analysis of the fracture of Q235 Q345 Steel Railroad Track Tie Plates Hot Forging Casting OEM
The body is sampled, and the as-cast and heat-treated castings are cut separately directly with a wire cutting machine, and the middle part is cut and prepared into several 10mm×15mm metallographic samples. Observe the metallographic structure with a metallographic microscope. It is the as-cast microstructure. It can be seen that the as-cast structure of the iron backing plate casting is ferrite + pearlite + Widmanstatite. Among them, the Widmanstatite structure is a continuous network, and a small amount of acicular Widmanstatten extends into the crystal grains. The research results show that when the carbon content of cast carbon steel exceeds 0.3%, the Widmanstatten structure will be produced when the grains are coarse. The main factors affecting the formation of Widmanstatten structure mainly include: austenite grain size, cooling rate and chemical composition. This Widmanstatten structure is brittle. Therefore, in order to improve the impact resistance of the backing plate casting, it must be eliminated by normalizing or annealing heat treatment. The factory originally used annealing heat treatment, which is the microstructure of the backing plate castings after annealing treatment, and there is a large amount of lath-shaped Widmanstatite. It can be judged that the annealing treatment did not eliminate a large amount of lath-shaped Widmanstatite. As a result, the existence of a large amount of lath-shaped Widmanite caused the backing plate castings to break when subjected to impact after being annealed. After careful inspection of the annealing equipment, it was found that the sealing performance of the annealing furnace door was poor, and the temperature control instrument of the annealing furnace had been damaged. Process requirements.
3. Improvement of iron pad production process Q235 Q345 Steel Railroad Track Tie Plates Hot Forging Casting OEM
Based on the above analysis results, improvement measures are proposed: re-repair the annealing equipment, improve the sealing performance of the annealing furnace door, and ensure that the temperature in the furnace meets the process requirements. After rectification, the original annealing process is still implemented, and the unqualified castings are re-heated. After metallographic inspection, it is found that the iron pad castings after annealing treatment no longer have a large amount of lath-like Widmanstatite. The impact test results show that there is no longer any quality problem that is prone to fracture when subjected to impact. Due to the simple structure of the piece, in order to simplify the process, shorten the production cycle, improve production efficiency, and reduce costs, according to the shape and structural characteristics of the casting, the normalizing process is adopted. The specifications are as follows: heating temperature 850 ℃; holding time 1h, air cooling to room temperature . After the factory adopted the normalizing process, the iron backing plate castings did not break under the same impact. The production cycle is shortened, the production efficiency is improved, and the cost is reduced.
A lock-type shock-absorbing rail iron backing plate combination structure is adopted, which includes an upper iron backing plate, an elastic backing plate, a lower iron backing plate and a locking sleeve structure. The elastic backing plate is clamped between the upper iron backing plate and the lower iron backing plate. Between the plates, the locking sleeve structure is used to lock the upper iron shim plate, the elastic shim plate and the lower iron shim plate, and the positioning nest is set on the cylinder structure of the lower iron shim plate, and the cylinder structure of the lower iron shim plate is in turn Pass through the elastic backing plate and the upper iron backing plate, and carry it on the first boss of the upper iron backing plate through the second boss, leaving a "C"-shaped gap in the outer ring of the first through hole, positioning and locking The sleeve is wedged into the "C"-shaped gap to be assembled into a combined structure of shock-absorbing steel rail and iron backing plate. The invention has a clever concept, good safety and reliability, good shock absorption effect, can effectively reduce the vibration of the iron backing plate combined structure, prevent the upper and lower iron backing plates from moving between the upper and lower iron backing plates, and can realize the upper locking of the iron backing plate combined structure, thereby Easy to install, aslo Use a peripheral edge trimming machine for iron pads. The trimming machine is equipped with horizontal and vertical rails for horizontally racking the iron pads. The material moving mechanism is used to change the direction of movement of the iron pads to make the iron pads The shift from the first horizontal rail to the first longitudinal rail enables the iron backing plate to move smoothly when moving horizontally and vertically. The iron backing plate is evenly in contact with the cutting tool when it is advanced horizontally, and the burrs on the surrounding iron backing plate are removed. Cut off to ensure the cutting quality, thereby overcoming the problem that the irregular shape of the bottom surface cannot slide directly on the workbench. Finally, the unloading mechanism is used to remove the iron backing plate from the positioning seat to complete the circumferential cutting of the iron backing plate. Edge processing.
Kingrail is specilized in supplying various tie plates to suit UIC,54kg,60kg,RE115-119,RE132-136,BS75A,80A,90A100A Steel rails, etc.
Other products supplied by Kingrail:
Rail car spares: wheels, axles, bearings, gears, couplers, etc
Railway Track materials: Tie plates, fishplates, screw spikes, bolts and nuts, steel rails and accessories, joint bar, gauge rod, etc