-
Steel Rail Wheels
-
Railway Wheel Set
-
Train Rail Wheels
-
Aluminum Alloy Wheels
-
Railway Spare Parts
-
Elastic Rail Clip
-
Railway Vehicles
-
Rail Wheel Axle
-
Steel Track Rail
-
Railway Fish Plates
-
Railway Tyres
-
Precision Forging Parts
-
Investment Casting Parts
-
Railway Track Fasteners
-
Railroad Track Cars
-
Rail Track Measuring Equipment
ODM Railway Steel Track Rail 6-12m Length Q235 55Q U71Mn Grade
Place of Origin | China |
---|---|
Brand Name | kingrail |
Certification | ISO |
Model Number | crane rail |
Minimum Order Quantity | Negotiable |
Price | Negotiable |
Packaging Details | standard export package, or as per customer request |
Delivery Time | 1-30 working days |
Payment Terms | L/C, D/A, D/P, T/T, Western Union, MoneyGram |
Supply Ability | 1000000000ton |
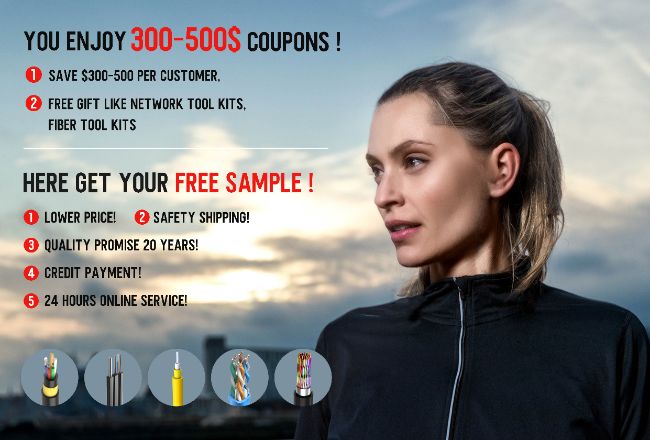
Contact me for free samples and coupons.
WhatsApp:0086 18588475571
wechat: 0086 18588475571
skype: sales10@aixton.com
If you have any concern, we provide 24-hour online help.
xStandard | AiSi, ASTM, Bs, DIN, GB, JIS | Bolt Hole Diameter | 22mm 24mm, As Customer's Requirement |
---|---|---|---|
Grade | Q235/55Q/U71Mn/75V/50Mn/45Mn | Length | 6-12m |
Rail Gauge | Normal Gauge | Specification | 4kg/m, 8kg/m 12kg/m, 15kg/m, 18kg/m, 22kg/m, 24kg/M,38-60 |
Highlight | ODM Steel Track Rail,U71Mn Steel Track Rail,12m Railway Steel Rail |
Introduction ov Railway Train Track International Standard Steel Light Rail, Heavy Rail, Crane Rail
Rails are the main components of railway tracks. Its function is to guide the wheels of the rolling stock to move forward, bear the huge pressure of the wheels, and transmit them to the sleepers. The rails must provide a continuous, smooth and least drag rolling surface for the wheels. In electrified railways or automatic blocking sections, the rails can also be used as track circuits.
Railway Train Track International Standard Steel Light Rail, Heavy Rail, Crane Rail specification
Light Rail
Type | Head Width(mm) | Height(mm) | Bottom Width | Web Thickness(mm) | Theory Weight(kg/m) | Grade | Length |
8kg | 25 | 65 | 54 | 7 | 8.42 | Q235B | 6M |
12kg | 38.1 | 69.85 | 69.85 | 7.54 | 12.2 | Q235B/55Q | 6M |
15kg | 42.86 | 79.37 | 79.37 | 8.33 | 15.2 | Q235B/55Q | 8M |
18kg | 40 | 90 | 80 | 10 | 18.6 | Q235B/55Q | 8-9M |
22kg | 50.8 | 93.66 | 93.66 | 10.72 | 22.3 | Q235B/55Q | 7-8-10M |
24kg | 51 | 107 | 92 | 10.9 | 24.46 | Q235B/55Q | 8-10M |
30kg | 60.33 | 107.95 | 107.95 | 12.3 | 30.1 | Q235B/55Q | 10M |
Heavy Rail
Head Width(mm) | Height(mm) | Bottom Width | Web Thickness(mm) | Theory Weight(kg/m) | Grade | Length | |
P38 | 68 | 134 | 114 | 13 | 38.73 | 45MN/71MN | |
P43 | 70 | 140 | 114 | 14.5 | 44.653 | 45MN/71MN | 12.5M |
P50 | 70 | 152 | 132 | 15.5 | 51.51 | 45MN/71MN | 12.5M |
P60 | 73 | 176 | 150 | 16.5 | 60.64 | U71MN | 25M |
Crane Rail
Head Width(mm) | Height(mm) | Bottom Width | Web Thickness(mm) | Theory Weight(kg/m) | Grade | Length | |
QU70 | 70 | 120 | 120 | 28 | 52.8 | U71MN | 12M |
QU80 | 80 | 130 | 130 | 32 | 63.69 | U71MN | 12M |
QU100 | 100 | 150 | 150 | 38 | 88.96 | U71MN | 12M |
QU120 | 120 | 170 | 170 | 44 | 118.1 | U71MN | 12M |
Specifications | Chemical Composition | Mechanical Properties | ||||||||
---|---|---|---|---|---|---|---|---|---|---|
Number | Classification | C | Si | Mn | P | S | Yield Strength | Tensile Strength | Elongation | |
range | range | range | max. | max. | min. | range or min. | min. | |||
% | % | % | % | % | N/mm2 (kgf/mm<span style="box-sizing: border-box; font-size: 12px; margin: 0px; padding: 0px; position: relative; line-height: 0; vertical-align: baseline; top: -0.5em; border: 0px; outline: 0px; background: transparent; color: inherit; font-family: "ヒラギノ角ゴ ProN W3", "Hiragino Kaku Gothic ProN", 游ゴシック, YuGothic, メイリオ, Meiryo, Verdana, "“Droid Sans" ",="" sans-serif;"="">2) | % | ||||
AREMA2011 Chapter 4"Rail" |
Standard Strength |
0.74−0.86 | 0.10−0.60 | 0.75−1.25 | 0.02 | 0.02 | 510 | 983min. | 10 | |
Intermediate strength |
0.72−0.82 | 0.10−1.00 | 0.70−1.25 | 0.02 | 0.02 | 552 | 1014min | 8 | ||
High strength | 0.74−0.86 | 0.10−0.60 | 0.75−1.25 | 0.02 | 0.02 | 827 | 1179min | 10 | ||
EN13674−2011 | R260 | 0.62−0.80 | 0.15−0.58 | 0.70−1.20 | 0.025 | 0.025 | − | 880min | 10 | |
R350HT | 0.72−0.80 | 0.15−0.58 | 0.70−1.20 | 0.02 | 0.025 | − | 1175min | 9 | ||
IRS T12−2009 | GR1080 | 0.60−0.80 | 0.10−0.50 | 0.80−1.30 | 0.03 | 0.03 | 460 | 1080min. | 10 | |
UIC860−R | GR900A | 0.60−0.80 | 0.10−0.50 | 0.80−1.30 | 0.04 | 0.04 | − | 880-1030 | 10 | |
JIS E1101−2001 |
Standard Rail |
37A | 0.55−0.70 | 0.15−0.35 | 0.60−0.90 | 0.045 | 0.05 | − | 690min.(70) | 9 |
40N | 0.63−0.75 | 0.15−0.30 | 0.70−1.10 | 0.03 | 0.025 | 800min.(82) | 10 | |||
50N | ||||||||||
60 | ||||||||||
JIS E1120−2007 |
HH340 HH370 |
0.72−0.82 | 0.10−0.55 | 0.70−1.10 | 0.03 | 0.02 | − | 1080(110) | 8 | |
0.10−0.65 | 0.80−1.20 | 1130(115) |
Head Hardened Rail(DHH Rails)
Rail classification
CHINA
The steel rails in our country can be divided into three categories: crane rails (crane rails), heavy rails and light rails based on the approximate weight of kilograms per meter:
① The crane rail is divided into four types: QU120, QU100, QU80, and QU70. The material is generally manganese steel. The largest single weight is QU120, which can reach 118kg/m.
② Heavy rail. According to the type of steel used, it is divided into: ordinary manganese-containing rails, copper-containing ordinary carbon steel rails, high-silicon copper-containing steel rails, copper rails, manganese rails, silicon rails, etc. There are mainly 38, 43 and 50kg. In addition, there are 45kg rails for a few lines, and 60kg rails have been planned for high-volume and high-speed lines. GB2585-81 stipulates the technical conditions of 38-50kg/m rail in my country, and its dimensions and codes are shown in Table 6-7-10.
In 2007, my country promulgated a new standard GB 2585-2007, in addition to 38 ~ 50kg/m, a new 60kg/m heavy rail and 75kg/m heavy machine rail.
Rail Type
The type of rail is expressed in kilograms of rail mass per meter of length. The rails used on my country's railways are 75kg/m, 60kg/m, 50kg/m, 43kg/m and 38kg/m.
The section shape of the rail adopts an I-shaped section with the best bending resistance, which is composed of three parts: the rail head, the rail waist and the rail bottom. In order to make the rail better withstand the forces from all sides and ensure the necessary strength conditions, the rail should have sufficient height, its head and bottom should have sufficient area and height, and the waist and bottom should not be too thin.
In addition, in order to meet the needs of structures such as turnouts, extra-large bridges and seamless lines, China Railway has also adopted special-section (I-shaped asymmetrical with the central axis) rails. The most commonly used rails are short and special section rails, referred to as AT rails.
Rail length
The standard lengths of Chinese rails are 12.5m and 25.0m. Extra-heavy and heavy-duty rails use 25.0m standard length rails, and other types of rails can use 12.5m25.0m standard length rails.
The "Interim Technical Conditions for 60kg/m Rail of 250km/h Passenger Dedicated Line" stipulates that the standard rail length of 250km/h passenger dedicated line (taking into account freight) is 100m.
There are three types of curvilinear shortened rails that are 40, 80, and 120mm shorter than the 12.5m standard rail, and three types that are 40, 80, and 160mm shorter than the 25.0m standard rail.
shape specification
Dimensions
The length and other geometric dimensions and tolerances of the rails are stipulated by the relevant standards for light and heavy rails in "8".
Appearance Quality
(1) The rail after rolling should be straight, and there should be no significant bending and twisting. The local bending and torsion of light and heavy rails and their correction deformation, the inclination of rail end faces, etc., shall not exceed the standard requirements.
(2) The surface of the rail should be clean and smooth, and there should be no defects such as cracks, scabs, scratches, etc.; there should be no shrinkage marks and interlayers on the end surface. The allowable defects on the overall surface of the light and heavy rails and the extent of their geometrical quantities shall not exceed the standards specified in the standard.
Rail damage
Rail damage refers to the occurrence of fractures, cracks and other damages that affect and limit the performance of the rail during use.
In order to facilitate the statistics and analysis of rail damage, it is necessary to classify the rail damage. According to the position of the damage on the rail section, the appearance of the damage and the cause of the damage, it is divided into nine categories and 32 types of damage, which are classified by two-digit numbers. cause of injury. The specific content of rail damage classification can be found in "Railway Public Works Technical Manual (Track)".
Rail breakage refers to one of the following situations: the full section of the rail is broken into at least two parts; the crack has penetrated the entire rail head section or the rail bottom section; there are pieces on the top surface of the rail with a length greater than 50mm and a depth greater than 10mm. The broken rail directly threatens the driving safety and should be replaced in time. Rail cracks refer to the separation of part of the rail material and the formation of cracks in addition to the fracture of the rail.
There are many types of rail damage, the common ones are wear, peeling and rail head nuclear damage, rail waist bolt hole cracks, etc. Several common rail damage situations are described below.
Rail wear
Rail wear mainly refers to the side wear and wave wear of the rail on the small radius curve. As for vertical wear, it is normal in general and increases with the increase of axle load and total passing weight. Improper setting of track geometry will speed up the vertical wear rate, which should be prevented and can be solved by adjusting the track geometry.
(1) Side wear
Flank wear occurs on outer strand rails with small radius curves and is one of the main types of damage on curves today. When the train is running on a curve, the friction and sliding of the wheel and rail are the root causes of the side wear of the outer rail. When the train passes through a small radius curve, the wheel-rail contact usually occurs at two points, and the side wear that occurs at this time is the largest. The size of the side wear can be expressed by the product of the guiding force and the impact angle, that is, the wear factor. Improving the conditions of the train passing through the curve, such as the use of wear-type wheel treads, the use of radial bogies, etc., will reduce the rate of side wear.
From the point of view of public works, the rail material should be improved, and wear-resistant rails should be used. For example, the wear resistance of high-hard rare earth rails is about 2 times that of ordinary rails, and that of quenched rails is more than 1 times.
Strengthen maintenance and repair, set appropriate gauge, outer rail superelevation and rail bottom slope, increase the elasticity of the line, apply oil on the side of the rail, etc., can reduce the effect of side wear.
(2) Wave wear
The wave-shaped wear refers to the wave-shaped uneven wear on the top surface of the rail, which is essentially a wave-shaped crush. Wave grinding will cause high wheel-rail dynamic effect, accelerate the damage of rolling stock and track components, and increase maintenance and repair costs; in addition, the violent vibration of the train will make passengers uncomfortable, and in severe cases will threaten driving safety; wave grinding is also noise. origin of. Serious wave grinding has occurred on some freight trunk lines in my country. Its development speed is faster than that of side grinding, and it has become the main reason for rail change.
Wave grinding can be divided into short wave (or ripple) and long wave (or wave) according to its wavelength. Ripple is periodic irregularity with a wavelength of about 50~100mm and an amplitude of 0.1~0.4mm; long wave is a periodic irregularity with a wavelength above 100mm and below 3000mm and an amplitude of less than 2mm.
Wave grinding mainly occurs on heavy-duty transportation lines, especially on coal and mine transportation lines. It also occurs on high-speed and high-passenger lines to varying degrees, and it is also common on urban subways. On railways with high train speeds, corrugation wear occurs mainly in straight lines and braking sections. Wave wear occurs mainly on heavy-duty transportation lines with low vehicle speeds, and generally occurs in curved sections. There are many factors that affect the occurrence and development of rail corrugation, involving many aspects such as rail material, line and locomotive conditions. Countries all over the world are devoted to the theoretical research on the causes of rail wave wear. There are dozens of theories about the genesis of wave mill, which can be roughly divided into two categories: dynamic genesis theories and non-dynamic genesis theories. In general, the dynamic action is the external cause of the rail corrugation, and the material properties of the rail are the internal cause of the corrugation. In fact, it is quite difficult to summarize all the causes of rail corrugation by analyzing only one aspect. Instead, we must take the vehicle and the rail as a system to study the formation of various vibrations, and conduct multi-faceted and multi-disciplinary research as a whole. In order to grasp the whole picture of the cause of wave grinding.
Grinding rails is now the most effective measure to eliminate wave grinding. In addition, there are the following measures to slow down the development of wave grinding: use continuous welding to eliminate rail joints and improve the smoothness of the rail; improve the rail material, use high-strength wear-resistant rails, improve the quality of heat treatment process, and eliminate rail residual stress; improve rail quality , improve the track elasticity, and make the vertical and horizontal elasticity continuous and uniform; keep the curve direction smooth, the superelevation setting is reasonable, the outer rail is oiled at the working side; the wheel-rail system should have sufficient resistance, etc.
(3) Allowable limits for rail wear
The allowable wear limit of the rail head is mainly determined by the strength and construction conditions. That is, when the rail wear reaches the allowable limit, firstly, it can ensure that the rail has sufficient strength and bending rigidity; secondly, it should ensure that the wheel flange does not collide with the joint splint in the most unfavorable situation. According to the "Rules for Maintenance of Railway Lines", according to the degree of wear and tear of the rail head, it is divided into two categories: minor injuries and serious injuries. The trough depth of the corrugated rail is more than 0.5mm, and the rail is lightly damaged.
Contact fatigue damage
The formation of contact fatigue damage can be roughly divided into three stages: the first stage is the change of the shape of the rail tread, such as unevenness of the rail tread and saddle wear at the weld, these irregularities will increase the impact of the wheel on the rail. ;The second stage is the destruction of the metal on the surface of the rail head. Due to the cold work hardening of the metal of the rail head tread, the hardness of the rail head working surface continues to increase. When the total mass is 150~200Mt, the hardness can reach HB360; Another change occurs. For carbon steel rails, when the total mass is 200~250Mt, micro-cracks are formed on the surface of the rail head. For a line with uneven elasticity, when the wheels and rails are obviously uneven, the tensile pressure on the top surface of the rail is almost equal. If there are micro-patterns, and the flexural stress and residual stress are the same, the strength of the rail will be greatly reduced. . The third stage is the formation of rail head contact fatigue. Due to insufficient metal contact fatigue strength and the repeated action of heavy-duty wheels, when the maximum shear stress action point exceeds the shear yield limit, this point will become a plastic region, and the wheel will Through the slip that will inevitably produce the metal microstructure, over a period of operation, this slip will accumulate and aggregate, eventually leading to the formation of fatigue cracks. The initiation and development of contact fatigue cracks will be accelerated with the increase of axle load, the transportation conditions of large volume, and the incompatibility of rail material and rail type.
The peeling near the fillet on the working edge of the rail head is mainly caused by the following three reasons: the peeling is caused by the longitudinal fatigue crack caused by the inclusion or the contact shear stress; the shear stress alternating cycle caused by the guide wheel on the curved outer rail promotes the outer rail Rail head fatigue leads to peeling; poor wheel and rail maintenance accelerates the development of peeling. Usually peeling will cause stress concentration in the notch area and affect the ride comfort, increase the dynamic impact, and promote the generation and development of cracks in the notch area. The existence of the notch area will also hinder the development of metal plastic deformation and reduce the plastic index of the rail.
Rail head nuclear injury is the most dangerous form of damage, which will break suddenly under the action of the train, seriously affecting the driving safety. The main reason for the nuclear damage of the rail head is that there are tiny cracks or defects (such as non-metallic inclusions and white spots) inside the rail head. The combination of stress causes fine cracks to nucleate first, and then develop around the rail head until the steel around the nucleation is not enough to provide sufficient resistance, and the rail breaks suddenly under the condition of a milli-yuan omen. Therefore, the defect of the internal material of the rail is the internal cause of nuclear damage, and the effect of external load is the external cause, which promotes the development of nuclear damage. The development of nuclear damage is related to the transportation capacity, axle load and speed, and the state of the line plane. In order to ensure the safety of driving, the rails should be inspected regularly.
Measures to slow down the contact fatigue damage of rails include: purifying rail steel and controlling the shape of debris; adopting quenched rails, developing high-quality heavy rails, and improving the mechanical properties of rail steels; reforming the old rail reuse system and using rails rationally; rail grinding; Rail steel material classification, track laying, etc.
For further information, welcome to contact!