-
Steel Rail Wheels
-
Railway Wheel Set
-
Train Rail Wheels
-
Aluminum Alloy Wheels
-
Railway Spare Parts
-
Elastic Rail Clip
-
Railway Vehicles
-
Rail Wheel Axle
-
Steel Track Rail
-
Railway Fish Plates
-
Railway Tyres
-
Precision Forging Parts
-
Investment Casting Parts
-
Railway Track Fasteners
-
Railroad Track Cars
-
Rail Track Measuring Equipment
Stainless Steel Investment Casting Parts Metal Stamping OEM
Place of Origin | China |
---|---|
Brand Name | Kingrail |
Certification | ISO |
Model Number | precision casting |
Minimum Order Quantity | Negotiable |
Price | Negotiable |
Packaging Details | standard export package, or as per customer request |
Delivery Time | 1-30 working days |
Payment Terms | L/C, D/A, D/P, T/T, Western Union, MoneyGram |
Supply Ability | 1000000ton |
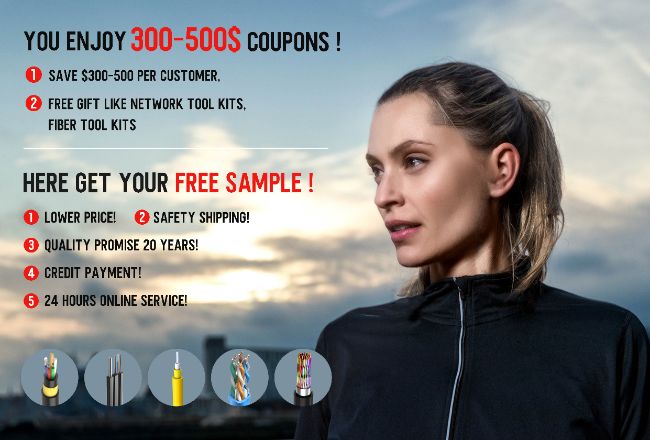
Contact me for free samples and coupons.
WhatsApp:0086 18588475571
wechat: 0086 18588475571
skype: sales10@aixton.com
If you have any concern, we provide 24-hour online help.
xMaterial | Stainless Steel, Carbon Steel, Alloy Steel | Specification | Customized |
---|---|---|---|
Product Name | Casting Stamping Parts | Application | Industry Machinery, Automotive, Electricity |
Process | Investment Casting | Surface Treatment | Zinc Plating, Painting, Powder Coating, Electro Polishing |
Testing Facilities | Spectrometer, CMM, Callipers, Micrometer, Projector Load | ||
Highlight | Stamping Stainless Steel Investment Casting Parts,OEM Stainless Steel Investment Casting Parts |
Stainless Steel Investment Casting Parts Metal Stamping OEM
The theoretical liquid metal forming of castings is often called casting, and the casting forming technology has a long history. As early as more than 5,000 years ago, our ancestors were able to cast copper and bronze products. Casting is the most widely used metal liquid forming process. It is a method of pouring liquid metal into the mold cavity, and after it cools and solidifies, a blank or part of a certain shape is obtained.
Liquid moldings account for a large proportion of machinery and equipment. Liquid moldings account for 70% to 90% of the total weight in machine tools, internal combustion engines, mining machinery, and heavy machinery; 50% to 70% in automobiles and tractors; Agricultural machinery accounts for 40% to 70%. The liquid forming process can be used so widely because it has the following advantages:
(1) It can manufacture blanks with complex inner cavity and shape. Such as various boxes, machine bed, cylinder block, cylinder head and so on.
(2) The process has great flexibility and wide adaptability. The size of the liquid molding is almost unlimited, and its weight can range from a few grams to several hundreds of tons, and its wall thickness can range from 0.5mm to 1m. Any metal material that can be melted into a liquid in the industry can be used for liquid molding. For very ductile cast iron, liquid forming is the only way to produce a blank or part.
(3) The cost of liquid molding parts is lower. Liquid molding can directly use waste parts and chips, and the equipment cost is low. At the same time, the machining allowance of liquid forming parts is small, which saves metal.
Castings are metal forming objects obtained by various casting methods, that is, the smelted liquid metal is injected into the pre-prepared casting mold by pouring, injection, suction or other casting methods, and after cooling, after grinding and other subsequent processing methods. , the resulting object of certain shape, size and properties.
There are many classification methods for castings: according to the different metal materials used, they are divided into steel castings, iron castings, copper castings, aluminum castings, magnesium castings, zinc castings, titanium castings, etc. And each type of casting can be further divided into different types according to its chemical composition or metallographic structure. For example, iron castings can be divided into gray iron castings, ductile iron castings, vermicular iron castings, malleable iron castings, alloy iron castings, etc.; according to different casting methods, castings can be divided into ordinary sand castings, metal castings, die castings , centrifugal castings, continuous castings, investment castings, ceramic castings, electroslag remelting castings, bimetal castings, etc. Among them, ordinary sand castings are the most widely used, accounting for about 80% of all castings. And aluminum, magnesium, zinc and other non-ferrous metal castings are mostly die castings.
performance
However, there are many processes for liquid metal forming, and it is difficult to precisely control, so that the quality of castings is not stable enough. Compared with forgings of the same material, due to the loose structure and coarse grains of liquid forming, defects such as shrinkage cavities, shrinkage porosity, and pores are easily generated inside. Its mechanical properties are low. In addition, the labor intensity is high and the conditions are poor. It has excellent mechanical and physical properties. It can have various comprehensive properties of strength, hardness and toughness, and can also have one or more special properties, such as wear resistance, high temperature and low temperature resistance, corrosion resistance, etc.
The weight and size range of castings are very wide. The lightest weight is only a few grams, the heaviest can reach 400 tons, the thinnest wall thickness is only 0.5 mm, the thickest can exceed 1 meter, and the length can be from a few millimeters to more than ten meters. It can meet the use requirements of different industrial sectors.
use
Castings are widely used and have been applied to hardware and the entire mechanical and electronic industries, and their uses are becoming an expanding trend. Specifically used, construction, hardware, equipment, construction machinery and other large machinery, machine tools, ships, aerospace, automobiles, locomotives, electronics, computers, electrical appliances,pouring process
In the casting process of machine tool bed castings, the principle of high temperature casting and low temperature casting should be followed during casting. Because raising the molten metal temperature is conducive to the complete melting of inclusions and the floating of slag, it is convenient for slag cleaning and degassing, and reduces the slag inclusion and porosity defects of machine tool castings; using a lower pouring temperature is conducive to reducing the amount of slag in the molten metal. The gas solubility, liquid shrinkage and the baking of the high temperature metal liquid on the surface of the cavity can avoid defects such as pores, sand sticking and shrinkage holes. Therefore, on the premise of ensuring that the mold cavity is filled, try to use a lower pouring temperature. The process of pouring molten metal from a ladle into a mold is called pouring. Improper pouring operation will cause machine tool casting defects such as insufficient pouring, cold insulation, pores, shrinkage holes and slag inclusion, and cause personal injury
Casting quality
It mainly includes appearance quality, inner quality and use quality. Appearance quality refers to the surface roughness, surface defects, dimensional deviation, shape deviation, and weight deviation of the casting; the internal quality mainly refers to the chemical composition, physical properties, mechanical properties, metallographic structure, and holes, cracks, inclusions, etc. Segregation and other conditions; service quality refers to the working durability of castings under different conditions, including wear resistance, corrosion resistance, shock resistance, fatigue, shock absorption and other properties, as well as machinability, weldability and other process properties.
Casting quality has a great influence on the performance of mechanical products. For example, the wear resistance and dimensional stability of machine tool castings directly affect the accuracy and life of the machine tool; the dimensions, accuracy and surface roughness of the impellers, casings, and inner cavities of hydraulic parts of various pumps directly affect the pump. And the working efficiency of hydraulic system, energy consumption and development of cavitation, etc.; the strength and resistance to cold and heat of internal combustion engine cylinder block, cylinder head, cylinder liner, piston ring, exhaust pipe and other castings directly affect the working life of the engine.
There are many factors that affect the quality of castings. The first is the design process of castings. When designing, in addition to determining the geometry and size of the casting according to the working conditions and metal material properties, the rationality of the design must also be considered from the perspective of the casting alloy and casting process characteristics, that is, the obvious size effect and solidification, shrinkage. , stress and other problems to avoid or reduce the occurrence of defects such as composition segregation, deformation and cracking of castings. The second is to have a reasonable casting process. That is, according to the structure, weight and size of the casting, the characteristics of the casting alloy and the production conditions, select the appropriate parting surface and modeling, core making method, and reasonably set the casting ribs, cold iron, riser and gating system. to ensure high quality castings. The third is the quality of raw materials for casting. The quality of metal charge, refractory material, fuel, flux, modifier, foundry sand, molding sand binder, coating and other materials is substandard, which will cause defects such as pores, pinholes, slag inclusion, and sticky sand in the casting, which will affect the appearance quality of the casting. and internal quality, the casting will be scrapped in severe cases. The fourth is process operation. It is necessary to formulate reasonable process operation rules, improve the technical level of workers, and make the process rules be implemented correctly.
In casting production, it is necessary to control and inspect the quality of castings. First of all, it is necessary to formulate process codes and technical conditions from raw materials and auxiliary materials to the control and inspection of each specific product. Each process is strictly controlled and inspected according to the process code and technical conditions. Finally, the quality inspection of the finished castings is carried out. To be equipped with reasonable testing methods and appropriate testing personnel. Generally, for the appearance quality of the casting, the surface roughness of the casting can be judged by comparing the sample blocks; the fine cracks on the surface can be checked by the coloring method and the magnetic powder method. The internal quality of castings can be checked and judged by methods such as audio frequency, ultrasound, eddy current, X-ray and γ-ray.
The defects of sand casting castings are: cold insulation, insufficient pouring, pores, sand sticking, sand inclusion, sand holes, and swelling sand.
1) Insufficient cold insulation and pouring: The liquid metal filling capacity is insufficient, or the filling conditions are poor. Before the cavity is filled, the molten metal will stop flowing, which will cause insufficient pouring or cold insulation defects in the casting. When the pouring is insufficient, the casting will not be able to obtain a complete shape; during cold isolation, although the casting can obtain a complete shape, the mechanical properties of the casting are seriously damaged due to the presence of incompletely fused seams.
Prevent insufficient pouring and cold isolation: increase the pouring temperature and pouring speed.
2) Porosity The gas does not escape in time before the liquid metal crusts, and the hole-like defects are generated in the casting. The inner walls of the pores are smooth, bright or slightly oxidized. After the pores are generated in the casting, its effective bearing area will be reduced, and stress concentration will be caused around the pores to reduce the impact resistance and fatigue resistance of the casting. Pores can also reduce the compactness of the casting, rendering some castings that require hydrostatic testing to be scrapped. In addition, porosity also adversely affects the corrosion resistance and heat resistance of the casting.
Prevent the generation of pores: reduce the air content in the molten metal, increase the air permeability of the sand mold, and add an air riser at the highest part of the cavity.
3) Sticky sand A layer of hard-to-remove sand adhered to the surface of the casting is called sticky sand. Sticky sand not only affects the appearance of castings, but also increases the workload of casting cleaning and cutting, and even affects the life of the machine. For example, when there is sticky sand on the surface of the cast teeth, it is easy to be damaged. If there is sticky sand in the machine parts such as pumps or engines, it will affect the flow of fluids such as fuel oil, gas, lubricating oil and cooling water, and will stain and wear the entire machine.
Prevent sand sticking: add pulverized coal to the molding sand, and apply anti-stick sand paint on the surface of the mold.
4) The grooves and scar defects formed on the surface of the casting by sand inclusion are very easy to occur when casting thick and large flat castings with wet molds.
Most of the parts that produce sand in the casting are in contact with the upper surface of the sand mold. The upper surface of the cavity is affected by the radiant heat of the molten metal, which is easy to arch and warp. When the warped sand layer is continuously scoured by the molten metal flow May break and shatter, remain in place or be carried to other locations. The larger the upper surface of the casting, the greater the volume expansion of the molding sand and the greater the tendency to form sand inclusions.
5) Sand holes are hole-like defects filled with molding sand inside or on the surface of the casting.
6) Expansion Sand It is a defect formed by the local expansion of the casting due to the movement of the mold wall under the pressure of the molten metal during pouring. In order to prevent sand expansion, the strength of the sand mold, the rigidity of the sand box, the pressure box force or tightening force when closing the box should be increased, and the pouring temperature should be appropriately lowered to make the surface of the molten metal crust earlier, so as to reduce the impact of the molten metal on the mold. pressure.
Quality Inspection
casting
The inspection of castings mainly includes dimensional inspection, visual inspection of appearance and surface, chemical composition analysis and mechanical property test. For castings that are more important or prone to problems in the casting process, non-destructive testing is also required, which can be used for ductile iron castings. Non-destructive testing techniques for quality testing include liquid penetrant testing, magnetic particle testing, eddy current testing, radiographic testing, ultrasonic testing and vibration testing.
1. Detection of casting surface and near-surface defects
1) Liquid Penetration Testing
Liquid penetrant testing is used to inspect various opening defects on the surface of castings, such as surface cracks, surface pinholes and other defects that are difficult to find with the naked eye. The commonly used penetrant inspection is coloring inspection, which is to soak or spray a colored (generally red) liquid (penetrant) with high penetrability on the surface of the casting, and the penetrant penetrates into the opening defect and quickly wipes off the surface penetrant. layer, and then spray an easy-to-dry display agent (also called developer) on the surface of the casting. After the penetrant remaining in the opening defect is sucked out, the display agent is dyed, which can reflect the shape of the defect, size and distribution. It should be pointed out that the accuracy of penetration testing decreases with the increase of the surface roughness of the tested material, that is, the brighter the surface, the better the detection effect. In addition to coloration detection, fluorescent penetrant detection is also a commonly used liquid penetrant detection method. It needs to be equipped with ultraviolet light for irradiation observation, and the detection sensitivity is higher than that of coloration detection.
2) Eddy current testing
Eddy current testing is suitable for inspecting defects below the surface that are generally not more than 6-7MM deep. Eddy current testing is divided into two types: the placed coil method and the through-type coil method. When the test piece is placed near the coil with the alternating current flowing, the alternating magnetic field entering the test piece can induce in the test piece an eddy current (eddy current) flowing in the direction perpendicular to the excitation magnetic field, and the eddy current will A magnetic field opposite to the excitation magnetic field is generated, so that the original magnetic field in the coil is partially reduced, thereby causing the coil impedance to change. If there is a defect on the surface of the casting, the electrical characteristics of the eddy current will be distorted, and the existence of the defect will be detected. The main disadvantage of the eddy current inspection is that the size and shape of the detected defect cannot be visually displayed. Generally, only the surface position and depth of the defect can be determined. , and it is not as sensitive as penetrant detection for detecting small open defects on the workpiece surface.
3) Magnetic particle inspection
Magnetic particle inspection is suitable for detecting surface defects and defects several millimeters deep below the surface. It requires DC (or AC) magnetization equipment and magnetic powder (or magnetic suspension) for inspection operations. Magnetizing equipment is used to generate a magnetic field on the inner and outer surfaces of the casting, and magnetic powder or magnetic suspension is used to reveal defects. When a magnetic field is generated within a certain range of the casting, the defects in the magnetized area will generate a leakage magnetic field. When the magnetic powder or suspension is sprinkled, the magnetic powder is attracted, so that the defects can be displayed. The defects displayed in this way are basically defects transverse to the magnetic field lines, and the long-shaped defects parallel to the magnetic field lines cannot be displayed. Therefore, the magnetization direction needs to be changed continuously during operation to ensure that each defect in an unknown direction can be detected. .
2. Detection of internal defects of castings
For internal defects, the commonly used nondestructive testing methods are radiographic testing and ultrasonic testing. Among them, the radiographic inspection effect is the best, it can obtain an intuitive image reflecting the type, shape, size and distribution of internal defects, but for large-thickness large castings, ultrasonic inspection is very effective, and the position of internal defects can be measured more accurately. , equivalent size and distribution.
1) Radiographic inspection (Micro focus XRAY)
X-rays or γ-rays are generally used as radiation sources for ray inspection, so equipment and other auxiliary facilities for generating ray are required. When the workpiece is placed in the ray field, the radiation intensity of the ray will be affected by the internal defects of the casting. The radiation intensity emitted through the casting varies locally with the size and nature of the defect, forming a radiographic image of the defect, which is imaged and recorded through a radiographic film, or detected and observed in real time through a fluorescent screen, or detected by a radiation counter. Among them, the method of imaging and recording by radiographic film is the most commonly used method, which is commonly referred to as radiographic inspection. The defect image reflected by radiography is intuitive, and the shape, size, number, plane position and distribution range of defects are all It can be shown, but the depth of the defect cannot be reflected in general, and special measures and calculations are needed to determine it. The international foundry industry network has applied the method of ray computed tomography, which cannot be popularized due to the expensive equipment and high use cost, but this new technology represents the future development direction of high-definition ray detection technology. In addition, the use of a microfocus X-ray system that approximates a point source actually eliminates the blurry edges created by larger focus devices, resulting in sharper image outlines. Using a digital imaging system can improve the signal-to-noise ratio of the image and further improve the clarity of the image.
2) Ultrasonic testing
Ultrasonic testing can also be used to inspect internal defects. It uses the propagation of sound beams with high-frequency sound energy inside the casting to generate reflections when they hit the internal surface or defects to find defects. The magnitude of the reflected acoustic energy is a function of the directivity and nature of the interior surface or defect and the acoustic impedance of such a reflector, so the acoustic energy reflected from various defects or interior surfaces can be applied to detect the presence of defects, wall thickness or surface the depth of the defect. As a widely used non-destructive testing method, ultrasonic testing has the main advantages of: high detection sensitivity, which can detect small cracks; large penetration ability, which can detect thick section castings. Its main limitations are: difficult to interpret reflection waveforms for discontinuous defects with complex contour dimensions and poor directivity; for undesired internal structures such as grain size, microstructure, porosity, inclusion content or fine dispersion Precipitates, etc., also hinder waveform interpretation; in addition, reference marks are required for detection
Lost Wax Investment Casting Parts Precision Steel Casting Parts custom metal stamping
How to repair casting defects:
The most fundamental focus of the method to solve the shrinkage defect of castings is "thermal balance". The method is:
(1) Rapid solidification is implemented in the thick parts and hot joints formed by the machine tool casting structure, which artificially causes the basic balance of the temperature field of the machine tool castings. Internal and external cold iron is used, and zircon sand, chromite sand or special coatings with large heat storage are used locally.
(2) Reasonable process design. The inner runner is located at the opposite wall of the machine tool casting, which is frequent and scattered. The molten metal that first enters the thick-walled part is solidified first, and the thin-walled part is solidified later, so that the uniform solidification is basically achieved everywhere. For machine tool castings with uniform wall thickness, use multiple sprues and vents. There are many inner runners, which are dispersed and evenly distributed, so that the overall heat is balanced. The air outlet is thin and many, that is, the exhaust is unobstructed and the heat is dissipated.
(3) Change the position of the inner runner
(4) The selection of modeling materials with large heat storage is extremely important for the production of anti-wear products with lost foam! Chromite sand replaces quartz sand and other sand types with low heat storage, which will achieve good results, and the micro-seismic is better after pouring!
(5) Low temperature and fast burning, open pouring system. Make the molten metal fill the mold quickly, smoothly and evenly. It depends on the situation.
(6) The machine tool casting of ductile iron has high strength, surface hardness ≧ 90, and high rigidity of the sand box, which is beneficial to eliminating shrinkage porosity.
(7) When the riser is needed, move the heat riser first and leave the heat section. If the riser is placed on the hot section, the size of the riser will be enlarged to form "heating on the heat". If it is not done well, not only the shrinkage porosity is difficult to remove, but also concentrated shrinkage cavities will be generated, which will reduce the process yield.
(8) The inclined placement and alloying of the casting mold are beneficial. Eliminating shrinkage defects of machine tool castings is a complex process of understanding and implementation. Based on the basic principle of "heat balance", scientific analysis of ju body castings should be made, a reasonable process plan should be formulated, suitable molding materials, tooling and correct operation should be selected and standardized. Then any shrinkage defects of machine tool castings can be solved.
Due to various factors, defects such as pores, pinholes, slag inclusions, cracks, and pits often appear. Commonly used repair equipment is argon arc welding machine, resistance welding machine, cold welding machine, etc. Casting defects that do not require high quality and appearance can be repaired by welding machines with high heat generation and high speed such as argon arc welding machines. However, in the field of precision casting defect repair, due to the great influence of argon welding heat, the repair will cause casting deformation, hardness reduction, blisters, local annealing, cracking, pinholes, wear, scratches, undercuts, or insufficient bonding force and internal Secondary defects such as stress damage. The cold welding machine just overcomes the above shortcomings, and its advantages are mainly reflected in the small heat affected area, the casting does not need to be preheated, and the cold welding repair at room temperature, so there is no deformation, undercut and residual stress, no local annealing, and no change to the metal of the casting. organization status. Therefore, the cold welding machine is suitable for surface defect repair of precision castings. The repair range of cold welding is the process of repeated melting and accumulation of welding repair points of Φ1.5-Φ1.2mm. In the process of repairing large-area defects, repair efficiency is the only factor that restricts its widespread application. For large defects, the combined application of traditional welding repair process and casting defect repair machine is recommended. But sometimes we don't have many defects, so we don't need to invest a lot of money. We can repair it with some repairing agents, which is convenient and simple. For example, for iron materials, we can use (Jinsucheng) JS902 to repair it. If it is not used up, it can be used later, which can save costs for our manufacturers, let our foundries invest more funds in improving the quality of the products themselves, and allow users to create more wealth.
3. Casting quality inspection results
Casting quality inspection results are usually divided into three categories: qualified products, repaired products, and rejected products.
1) Qualified products refer to castings whose appearance quality and internal quality meet relevant standards or technical conditions for delivery acceptance;
2) Reworked products refer to castings whose appearance quality and internal quality do not fully meet the standards and acceptance conditions, but are allowed to be repaired, and after repairs, they can meet the standards and casting delivery acceptance technical requirements;
3) Scrap refers to castings that are unqualified in appearance quality and internal quality, and are not allowed to be repaired or still fail to meet the standards and technical requirements for casting delivery acceptance after repairing. Waste is further divided into internal waste and external waste. Internal waste refers to the waste castings found in foundries or foundries; external waste refers to the waste found after the casting is delivered, and the economic loss caused by it is far greater than that of internal waste. [2]
Factors Affecting the Solidification Mode of Castings
There are many methods of solidification of castings. During the solidification process of the casting, the section is generally divided into three zones: 1-solid phase zone 2-solidification zone 3-liquid phase zone has a greater influence on the solidification zone is the width of the solidification zone, and the solidification method is divided accordingly. First, intermediate solidification: the solidification of most alloys is between layer-by-layer solidification and paste solidification. Second, layer-by-layer solidification: pure metal, eutectic composition alloys have no solidification zone during solidification, and the liquid and solid two phases are clearly separated by a boundary. Direct access to the center. Third, mushy solidification: the crystallization temperature range of the alloy is very wide. During a certain period of solidification, there is no solid layer on the surface of the casting, and the solidification zone runs through the entire section, first mushy and then solidified. Relevant experts said that the factors affecting the solidification mode of castings are summarized: First, the temperature gradient of the castings. When the crystallization temperature range of the alloy is constant, the width of the solidification zone depends on the temperature gradient of the inner and outer layers of the casting. The smaller the temperature gradient, the wider the solidification zone. (The temperature difference between inside and outside is large, the cooling is fast, and the solidification zone is narrow). Second, the crystallization temperature range of the alloy. Small range: The solidification zone is narrow, and it tends to solidify layer by layer. Such as: sand casting, low carbon steel solidification layer by layer, high carbon steel paste solidification.
Casting defect repairing agent is a two-component, cement-like, room temperature curing polymer resin glue, polymer metal composite cold welding repair material with metal and alloy as reinforcing filler. It has high bonding strength with metal, and can basically keep the same color, and has the characteristics of wear resistance, corrosion resistance and aging resistance. The cured material has high strength, no shrinkage, and can be processed by various types of machinery. It has excellent properties such as wear resistance, oil resistance, water resistance, and various chemical corrosion resistance, and can withstand high temperature of 120 ° C.
use
Casting defect repair agent is a high-performance polymeric metal material obtained by compounding various alloy materials and modified toughening heat-resistant resins. It is suitable for repairing various metal castings and various castings with defects larger than 2mm. , crack, wear, corrosion repair and bonding. It is generally used for the repair of various casting defects with less stringent color requirements. It has high strength and can be machined with the base material.
How to detect
The properties of the casting itself directly affect the quality of the processing, and the hardness value is an important indicator to determine the processing of the casting.
1) Brinell hardness: It is mainly used to measure the hardness of castings, forgings, non-ferrous metal parts, hot-rolled billets and annealed parts. The measurement range is ≯HB450.
2) Rockwell hardness: HRA is mainly used for high hardness test pieces, to measure the hardness of materials and surface hardness above HRC67, such as cemented carbide, nitrided steel, etc., the measurement range is HRA>70. HRC is mainly used for hardness measurement of steel parts (such as carbon steel, tool steel, alloy steel, etc.) after quenching or tempering, and the measurement range is HRC20~67.
3) Vickers hardness: used to measure the hardness of thin parts and steel plate parts, and can also be used to measure the hardness of surface hardened parts such as carburizing, cyanidation, and nitriding.
Main Testing and Inspection Device
No. | Device | Type | Qty | Status | Note |
1 | End quenching machine | DZJ-I | 1 | working | Testing |
2 | Electric resistance furnace | SX2-8-12 | 2 | working | Testing |
3 | Inverted metallurgic microscope | 4XCE | 1 | working | Inspection |
4 | High temperature box resistance furnace | SX2-4-13 | 1 | working | Testing |
5 | Automatic digital display Rockwell hard-tester | 200HRS-180 | 1 | working | Inspection |
6 | Electronic Brinell hardness tester | THB-3000 | 1 | working | Inspection |
7 | HR-150B Rockwell hardness tester | HR-150B | 1 | working | Inspection |
8 | Rapid multi-element analyzer | JS-DN328 | 1 | working | Inspection |
9 | Electric arc furnace | JSDL-8 | 1 | working | Testing |
10 | Rapid multi-element analyzer(C & S) | JS-DN328 | 1 | working | Inspection |
11 | Infrared thermometer | AR872 | 2 | working | Inspection |
12 | Portable chemical composition analyzer | AR872 | 2 | working | Inspection |
13 | Test specimen sampler | KW30-6 | 1 | working | Inspection |