-
Steel Rail Wheels
-
Railway Wheel Set
-
Train Rail Wheels
-
Aluminum Alloy Wheels
-
Railway Spare Parts
-
Elastic Rail Clip
-
Railway Vehicles
-
Rail Wheel Axle
-
Steel Track Rail
-
Railway Fish Plates
-
Railway Tyres
-
Precision Forging Parts
-
Investment Casting Parts
-
Railway Track Fasteners
-
Railroad Track Cars
-
Rail Track Measuring Equipment
Thick 30mm Investment Casting Parts Wheel ODM For Ford Endeavour Road Shaker
Place of Origin | China |
---|---|
Brand Name | Kingrail |
Certification | ISO |
Model Number | precision casting |
Minimum Order Quantity | Negotiable |
Price | Negotiable |
Packaging Details | standard export package, or as per customer request |
Delivery Time | 1-30 working days |
Payment Terms | L/C, D/A, D/P, T/T, Western Union, MoneyGram |
Supply Ability | 1000000ton |
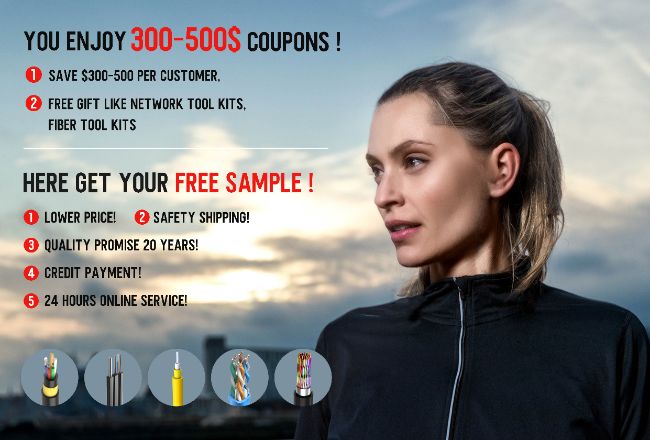
Contact me for free samples and coupons.
WhatsApp:0086 18588475571
wechat: 0086 18588475571
skype: sales10@aixton.com
If you have any concern, we provide 24-hour online help.
xMaterial | Stainless Steel, Carbon Steel, Alloy Steel | Specification | Customized |
---|---|---|---|
Product Name | Casting Stamping Parts | Application | Industry Machinery, Automotive, Electricity |
Process | Investment Casting | Surface Treatment | Zinc Plating, Painting, Powder Coating, Electro Polishing |
Testing Facilities | Spectrometer, CMM, Callipers, Micrometer, Projector Load | ||
Highlight | 30mm Investment Casting Parts,ODM Investment Casting Parts,Road Shaker Investment Casting Parts |
Production of PCD 6x139.7-93.1 Thick 30mm Forged Alloy Car Wheel Hub Spacer For Ford Endeavour and Road Shaker
Aluminum casting refers to equipment and devices of pure aluminum or aluminum alloy obtained by casting. Generally, a sand mold or a metal mold is used to pour the aluminum or aluminum alloy heated into a liquid state into the mold cavity, and the obtained aluminum parts or aluminum alloy parts of various shapes and sizes are usually called aluminum die castings.
Business Type | Factory/Manufacturer |
Service |
CNC machining Stamping Laser cutting Sheet metal fabrication Die Casting |
Material |
1). Aluminum: AL 6061-T6, 6063, 7075-T etc. 3). Steel: 4140, Q235, Q345B,20#,45# etc. |
Surface Treatment |
Sandblasting, anodize color, blackenning, zinc/nickl plating, polish, power coating, passivation PVD, titanium plating, etc. |
Main equipment |
CNC machining center(milling), CNC lathe, grinding machine, cylindrical grinder machine, drilling machine, laser cutting machine,etc. |
Drawing format | STEP,STP,GIS,CAD,PDF,DWG,DXF etc or samples. |
MOQ | Small order acceptable |
Delivery time | 5-30 days depends on quantities. |
QC | 100% inspection, ROHS. |
Tolerance | +/-0.01mm ~ +/-0.05mm |
Surface roughness |
Ra 0.1~3.2 |
Strenghth of Kingrail casting production line
KINGRAIL designed an aluminum alloy forging and a method for improving the uniformity of the aluminum alloy forging, wherein the method for improving the uniformity of the aluminum alloy forging includes: step 1), performing solution treatment on the aluminum alloy forging; step 2), the step of 1) The treated aluminum alloy forging is subjected to quenching treatment; step 3), the aluminum alloy forging treated in step 2) is subjected to cold compression treatment, and the time interval between step 2) and step 3) is 1h to 4h; step 4 ), performing aging treatment on the aluminum alloy forging treated in step 3). This scheme optimizes the time interval between quenching and cold compression, so as to have a positive impact on the uniformity of the aluminum alloy deformation treatment process, improve the uniformity of the deformation heat treatment structure, and finally improve the performance of aluminum alloy forgings
A fully automatic casting production line, which includes a work surface set on the ground; a low-pressure machine, which is set on the work surface and arranged laterally and performs die-casting of castings; a casting reclaiming transfer mechanism, which is set on the work surface and clamps The castings processed by the low-pressure machine are transferred and placed in the cooling equipment; the cooling equipment is fixedly arranged on the work table and the castings clamped by the casting material reclaiming and transferring mechanism are cooled and processed; the core removal station, which is fixed Set on the work table and process the castings clamped by the casting transfer mechanism from the cooling equipment, power milling, which is fixed on the work table and processed by the castings processed by the sawing station; product discharge The platform is fixedly arranged on the work table and conveys the power-milled products. In the present invention, a robot is used to replace manual operation, which saves manpower and costs, and especially improves the quality of products.
Advantages: The moving and flipping method of aluminum alloy castings in the sand removal equipment is too simple, so that the sand removal effect of aluminum alloy castings will decrease, and in order to improve the sand removal effect of aluminum alloy castings, the The sand removal time is long, which will make the sand removal effect difficult to achieve better, and the sand removal efficiency will also decrease, which will affect the output of aluminum alloy castings; it is difficult to clean the inner wall of the sand removal equipment in time, resulting in sand removal. The residual grit on the inner wall of the equipment gradually accumulates.
Main Testing and Inspection Device of PCD 6x139.7-93.1 Thick 30mm Forged Alloy Car Wheel Hub Spacer For Ford Endeavour and Road Shaker
No. | Device | Type | Qty | Status | Note |
1 | End quenching machine | DZJ-I | 1 | working | Testing |
2 | Electric resistance furnace | SX2-8-12 | 2 | working | Testing |
3 | Inverted metallurgic microscope | 4XCE | 1 | working | Inspection |
4 | High temperature box resistance furnace | SX2-4-13 | 1 | working | Testing |
5 | Automatic digital display Rockwell hard-tester | 200HRS-180 | 1 | working | Inspection |
6 | Electronic Brinell hardness tester | THB-3000 | 1 | working | Inspection |
7 | HR-150B Rockwell hardness tester | HR-150B | 1 | working | Inspection |
8 | Rapid multi-element analyzer | JS-DN328 | 1 | working | Inspection |
9 | Electric arc furnace | JSDL-8 | 1 | working | Testing |
10 | Rapid multi-element analyzer(C & S) | JS-DN328 | 1 | working | Inspection |
11 | Infrared thermometer | AR872 | 2 | working | Inspection |
12 | Portable chemical composition analyzer | AR872 | 2 | working | Inspection |
13 | Test specimen sampler | KW30-6 | 1 | working | Inspection |
Main Testing and Inspection Device
No. | Device | Type | Qty | Status | Note |
1 | End quenching machine | DZJ-I | 1 | working | Testing |
2 | Electric resistance furnace | SX2-8-12 | 2 | working | Testing |
3 | Inverted metallurgic microscope | 4XCE | 1 | working | Inspection |
4 | High temperature box resistance furnace | SX2-4-13 | 1 | working | Testing |
5 | Automatic digital display Rockwell hard-tester | 200HRS-180 | 1 | working | Inspection |
6 | Electronic Brinell hardness tester | THB-3000 | 1 | working | Inspection |
7 | HR-150B Rockwell hardness tester | HR-150B | 1 | working | Inspection |
8 | Rapid multi-element analyzer | JS-DN328 | 1 | working | Inspection |
9 | Electric arc furnace | JSDL-8 | 1 | working | Testing |
10 | Rapid multi-element analyzer(C & S) | JS-DN328 | 1 | working | Inspection |
11 | Infrared thermometer | AR872 | 2 | working | Inspection |
12 | Portable chemical composition analyzer | AR872 | 2 | working | Inspection |
13 | Test specimen sampler | KW30-6 | 1 | working | Inspection |