-
Steel Rail Wheels
-
Railway Wheel Set
-
Train Rail Wheels
-
Aluminum Alloy Wheels
-
Railway Spare Parts
-
Elastic Rail Clip
-
Railway Vehicles
-
Rail Wheel Axle
-
Steel Track Rail
-
Railway Fish Plates
-
Railway Tyres
-
Precision Forging Parts
-
Investment Casting Parts
-
Railway Track Fasteners
-
Railroad Track Cars
-
Rail Track Measuring Equipment
Machined Aluminum Wheel Forging , Kingrail OEM 6061 T6 Cast Aluminum Rims
Place of Origin | China |
---|---|
Brand Name | Kingrail |
Certification | ISO |
Model Number | KR-TF-03 |
Minimum Order Quantity | 1 pc |
Price | Negotiable |
Packaging Details | standard export package, or as per customer request |
Delivery Time | 1-30 working days |
Payment Terms | L/C, D/A, D/P, T/T, Western Union, MoneyGram |
Supply Ability | 1000000ton |
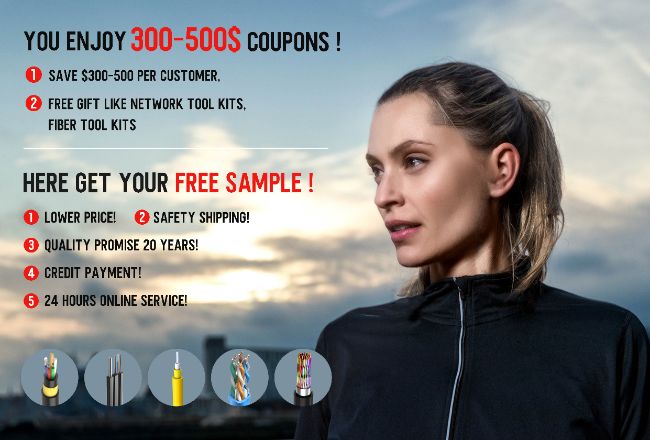
Contact me for free samples and coupons.
WhatsApp:0086 18588475571
wechat: 0086 18588475571
skype: sales10@aixton.com
If you have any concern, we provide 24-hour online help.
xStandard | AISI, GB, ASTM, DIN | Machining Tolerance | 0.005mm-0.01mm-0.1mm |
---|---|---|---|
Material | Alloy Steel/ASTM 148 | Process | Hot Forging,Cold Forging,Warm Forging |
Molding Style | Forging | Surface Treatment | Polishing,Plating,Powder Coating, Hot Galvanizing, |
Highlight | Kingrail Aluminum Wheel Forging,OEM Aluminum Wheel Forging,6061 T6 Cast Aluminum Rims |
monoblock precision-machined forged 6061-T6 aluminum centers and rim for luxury vehicle applications
The invention relates to a production process of high-strength and high-toughness forged aluminum alloy wheels, which relates to the technical field of aluminum alloy wheels. The process is roughly aluminum alloy bar selection, aluminum alloy bar preparation, aluminum alloy bar heating, pre-forging process, forming forging process, flaring forging process, spinning and drawing process, heat treatment process, lathe roughing, machining center Drilling process. Compared with the prior art, by improving the aluminum alloy production process, the present invention controls the process conditions more reasonably according to the wheel structure and stress characteristics, and the grain structure is refined and arranged in an orderly manner during the forging process of the aluminum alloy bar. The original internal structure of the aluminum alloy is obtained. The hardness of the wheel manufactured by this process can reach 120-130HB, the tensile strength is 400-450MPa, and the elongation after breaking is 12-14%. Compared with the traditional wheel, the weight is reduced by 17-22Kg.
The raw material is T6-6061(or 6082,or 6110), main production process is Forging--Spinning---Heat treatment---CNC----Powder coat
A final press forging process for an axle box body of a rail vehicle bogie, comprising: heating a pre-press forging box blank to 420°C-440° C, and maintaining the temperature for a duration of more than or equal to 210 minutes, and heating a pre-press forging die to 350°C-450°C, the heating time is greater than or equal to 8 hours; the cuboid-shaped ingot is pre-forged through the pre-press forging die, and the pre-forging temperature is 420° C-440° C, and the final forging is performed. The temperature is greater than or equal to 380 ℃ to form the axle box. The rail vehicle bogie axle box body final pressure forging process provided by the invention, the aluminum alloy obtained by the method, the bogie axle box body produced by the aluminum alloy has high tensile strength, yield strength and elongation rate, which can meet the requirements of high-speed railway bogies Mechanical performance requirements of the axle box.
monoblock precision-machined forged 6061-T6 aluminum centers and rim for luxury vehicle applications
For the forging and heat treatment process of free forgings, weigh the following raw materials by weight: Cr: 0.5%-1.0%, Mg: 5.0%-7.5%, Zn: 0.05%-0.10%, Ti: 0.03%-0.05%, Cu: 1.5 %? 2.0%, Fe: 0.10%? 0.15%, slag cleaning agent: 3.5%? 5.0%, and the balance is Al; the slag cleaning agent can remove the hydrogen and floating oxidation slag inclusions in the aluminum alloy liquid, and make the alloy liquid more Pure, its own strong adsorption properties can adsorb slag inclusions and improve the purity of aluminum alloys, and the chemical structure of the added sodium hexafluoroaluminate is similar to that of alumina. The surface tension when it is in contact with the aluminum melt, and then the aluminum oxide in the aluminum alloy liquid is removed; the addition of sodium fluoride can erode the metal on the interface between the aluminum oxide and the aluminum, so that the oxide film falls off and falls into the flux. Aluminum alloy for purification.
Monoblock precision-machined forged 6061-T6 aluminum centers and rim for luxury vehicle applications
|
|
Main Process
|
Material Cutting, Material Heating, Forging, Heat Treatment, Blasting&Polishing, CNC Machining
|
Material
|
Aluminum, Carbon Steel, Stainless Steel Brass, ,DC53 or as customer request
|
Surface Treatment
|
Shot/sand blast, Polishing, Surface Passivation, Primer Painting , Powder Coating, ED- Coating, Chromate Plating, Zinc Plating, Dacromat Coating, Finish Painting
|
Application
|
1. Construction: lifting anchors for precast concrete, spherical head anchors
2. Automotive industry: piston, connecting rods, cams, camshafts, crankshafts 3. Heavy machinery: Rock breaker, excavator parts 4. Energy: Anvil, gate valve, wellhead control EQP, wellhead EQP 5. Defense: Black receiver, aluminum trigger guards and receivers 6. Truck: Cylinder heads, oil sump, clutch housing, front and rear brake calipers. |
Machining Process
|
CNC Machining/ Lathing/ Milling/ Turning/ Boring/ Drilling/ Tapping/ Broaching/ Reaming /Grinding/Honing and etc.
|
Machining Tolerance
|
From 0.005mm-0.01mm-0.1mm
|
Drawing Format
|
jpg/.pdf/.dxf/.dwg/.igs./.stp/x_t. etc
|
Testing Machine
|
CMM, Digital Height Gauge, Caliper, Coordinate Measuring Machine, Projecter Machine, Roughness Tester, Hardness Tester and so on
|
Certificate | ISO9001, CE, TUV, SGS or as your requirement to do test by the third party |
Delivery time | 10-15 days for sample,
35-40 days for bulk order |
Packing | Plywood pallet, plywood box or as per your requirement |
Quality Control | Conducted by ISO9001 System and PPAP Quality control documents |
Service | Warm and quick response service provided by the professional
Export Sales Team with many years' experience in handling exports to the US, Europe, Japan and other countries and regions. |
Extra Product Description of Train Forged Aluminum Wheel 4WD T6-6061(or 6082,or 6110) material heat treatment
Accurate in reading drawings & Fast in delivery & Exact dimension control & 100% quality control & OEM Service & Strict material inspection & Prompt quote & lead time guarantee | |
1. Product Name: | Sand Casting train wheel forging |
2. Material: | Carbon Steel, Alloy Steel, Stainless Steel,Grey iron,Ductile iron,High Chrome iron ,High Manganese steel |
3. Material Standard: | ASTM,AISI,ASME,SAE,NF EN,DIN EN,ISO,,BS EN,SS,etc. |
4. Items: | FOB Tianjin or Shanghai,China |
5. Lead time: | 30~40 days |
6. Place of origin | Maanshan, China |
7. Software for specification drawings: | PDF, Auto CAD, Solidworks, JPG, ProE,etc. |
8. Main production equipments: | Wax injection, CNC-machine-center, Lathe, Milling machine,Drilling machine,Boring Lathe,Grinding Machine, Heat treatment Furnace. |
9. Heat Treatment Machine: | Mesh-Belt-Furnace,Carburizing Quench Furnace,Chamer Furnace,etc. |
10. Surface Treatment: | Cold/Hot Zn Plating,Blackening Treatment(Salt Spray Test 48-96 hours),Ni Plating,Cr Plating,Spraying Undercoat,Anti-Rust Paint,Surface Paint,Plastic Paint,Coated Anti-Rust Water,Anti-oil,etc. |
11. Surface Heat Treatment: | Medium Frequence Quenching,High Frequence Quenching and Carburizing and Quenching,Oil Quenching,Water quenching,Normalizing,Temper,Annealing,etc. |
12. Dimension Inspection: | Calipers,Height Laugue,Micrometer Calipers,Inside Caliper Gauge,Angle and R Gauge,Three coordinates measuring instrument. |
13. Productivity: | 5000 pcs / year |
14. Packaging: | Wooden package after mandatory treatment or other |
15.They are using for mining equipment,Construction equipment,Agricultural equipment and others. | |
16. We make precision casting,investment casting and Sand casting in Ningbo, China | |
17. Export Markets: Portugal Grey Iron casting parts; America, U.S.A. United States Grey Iron casting parts; Canada Grey Iron casting parts; U.K. Brazil, Spain Grey Iron casting parts; Portugal Grey Iron casting parts; Portugal Grey Iron casting parts; Spain Grey Iron casting parts Spain Espana Grey Iron casting parts; Holand Grey Iron casting parts Portugal Grey Iron casting parts; Danmark Grey Iron casting parts Portugal Grey Iron casting parts; Spain Grey Iron casting parts | |
18. We can check with gauge: |