-
Steel Rail Wheels
-
Railway Wheel Set
-
Train Rail Wheels
-
Aluminum Alloy Wheels
-
Railway Spare Parts
-
Elastic Rail Clip
-
Railway Vehicles
-
Rail Wheel Axle
-
Steel Track Rail
-
Railway Fish Plates
-
Railway Tyres
-
Precision Forging Parts
-
Investment Casting Parts
-
Railway Track Fasteners
-
Railroad Track Cars
-
Rail Track Measuring Equipment
Hot Steel Forged Rail Wheels 12 Inches 4140 Material 490 Hb Hardness
Place of Origin | China |
---|---|
Brand Name | kingrail |
Certification | ISO |
Model Number | 750mm |
Minimum Order Quantity | Negotiable |
Price | Negotiable |
Packaging Details | standard export package, or as per customer request |
Delivery Time | 1-30 working days |
Payment Terms | L/C, D/A, D/P, T/T, Western Union, MoneyGram |
Supply Ability | 1 million pcs/year |
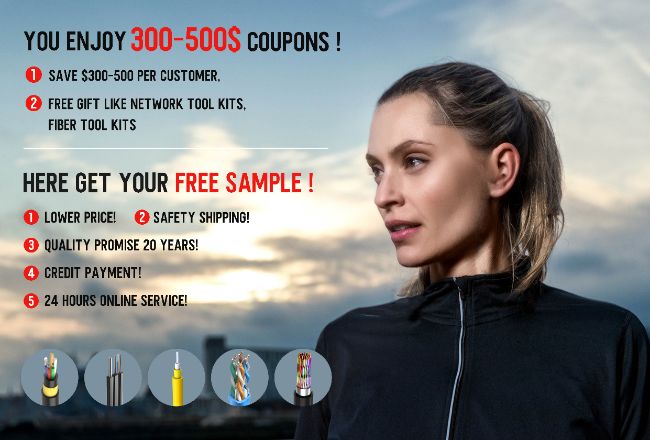
Contact me for free samples and coupons.
WhatsApp:0086 18588475571
wechat: 0086 18588475571
skype: sales10@aixton.com
If you have any concern, we provide 24-hour online help.
xDiameter | 0-1450mm | Production | Casting And Forging As Per Customer Request |
---|---|---|---|
Material | 4140,42CrMo,60E, Etc | Inspection | 100% Inspection, UT,MT, Sizes, Mechanical Property |
Progress | Forging-machining-inspection-heat Treatment-machining-inspection | Hardness | 150-560HB |
Application | Railway, Rail Cart Or Shipyard,Rail Road Vehicles, Railcar | Max. Capacity | Up To 500ton |
Export Area | Germany, French, UK, US, South Korea, South Africa, Etc | Sizes | As Per Customer Drawing |
Highlight | Hot Steel Forged Rail Wheels,12 Inches Railway Wheels |
Detailed specification of Hot Steel Forged Rail Wheels 12 Inches 4140 Material 490 Hb Hardness
double and single flange mobile rail steel wheel
- 1. Material: cast steel or cast iron;
Carbon steel:C45, C50, C55, C60, 4330, C35, 65Mn
Alloy steel:4140, 42CrMo, 40CrNiMo, 4340, 34CrNiMo6
- 2. Constitute: two wheels, one axle, four bearings, and other parts;
- 3. Loading capacity: 1-300 tons, can be customized.
- 4. The type of the wheels: single flange wheel, double flange wheel, hollow wheel sets and solid wheel sets;
- 5. The diameter of the wheels: 300mm, 350mm, 400mm, 450mm;500mm; 900mm, etc.
- 6) Heat treatment: normalizing, Q&T ,Surface and rim quenching with depth: 5-20mm
7) Measuring & testing equipment: Projecting profile, roughness tester, hardness tester, concentricity tester ect, UT ,MT
8) Size:Customized designs are available.
9) Inspection:In-house and the third party.
The difference and comparison of forged wheels and cast wheels
1. From the perspective of object shape transformation:
Casting a wheel is to liquefy solid metal, and then put the liquid metal without shape into a mold to get something of different shape (solid-liquid-solid).
Forged wheels are solids that turn one shape solid into another. That is, solids change from one shape to another at high temperatures (solid-solid).
2. In terms of focus:
Casting a wheel is the process of casting molten metal into a model to obtain a casting. The foundry major focuses on the metal smelting process and the control of the process during the casting process
Forged wheels are plastic forming in solid state, which can be divided into hot working and cold working. Such as extrusion, drawing, pier thickening, punching, etc. belong to forging.
3. In terms of molding speed:
Casting the wheel is a one-time molding, the molten liquid metal fills the cavity and cools, and pores are easily generated in the middle of the part.
Forged wheels are formed slowly, mainly by extrusion at high temperature. The grains in the part can be refined.
4. In terms of performance differences:
Cast steel is brittle in performance and cannot be heat treated.
Forged steel has a finer structure, good toughness and strength, and can be subjected to various heat treatments.
Advantages of cast wheels: low price, short production cycle; disadvantages: low strength, easy to shatter after severe impact; enough for family car owners who do not have too many requirements for control and pursue economical benefits.
Advantages of forged wheels: light weight, good heat dissipation, high strength, not easy to be crushed after impact, higher safety, strong plasticity, and can be customized at will; Disadvantages: slightly higher price, long production cycle; forged wheels are suitable for the pursuit of performance, control and individuality.
Strength of Railway wheel dimensions for Catenary and Track maintenance vehicles
1. Forging production, longer lifespan, for smaller quantity, free forging, for big quantity, precision forging with mould
2. Diameter: 0-1450mm, 6",8",10",12",14",16",20",24",28",30",34",36",40",42",etc
3.100% inspection before delivery
Usage of Hot Steel Forged Rail Wheels 12 inches railway wheels 4140 material 490 hb hardness precision hole of 0.01mm
Train, railcars, light rail, street car, metro, freight car, railway wagon for mining, rail trucks, ballast rail cars, Hy-rail hirail cars, etc
The Production Railway Wheels Process Railway wheel dimensions for Catenary and Track maintenance vehicles
1. Wheels Steel Melting 2. Round Billet Sawing Cutting 3. Heating 4. Phosphorus 5. Stamping Forming 6. Rolling 7. Bending Punch 8. Hot Stamping 9. Laser Measurement 10. Drop Stack 11. Roughing 12.Hardening 13.Tempering 14. Sampling 15. Pre-processing 16. Finishing 16. The Cold Print 17. Static Equilibrium 18. The Cold Print 19. Hardness Testing 20. Ultrasonic Testing 21. Magnetic Particle Testing 22. Shot Peening 23. Painting Packaging
Hot Steel Forged Rail Wheels 12 Inches 4140 Material 490 Hb Hardness
Main Production Equipment List
No. | Equipment | Type | Qty | Status | Note |
1 | Vertical lathe | VTC6070 | 36 | working | Finishing workshop |
2 | VMC | AVL-860 | 3 | working | Finishing workshop |
3 | VMC | VMC850B | 14 | working | Finishing workshop |
4 | Multi-function machine | HTC2050n | 20 | working | Finishing workshop |
5 | CAK | 5085di | 10 | working | Finishing workshop |
6 | Steyr CNC lathe | CK7520ACK50 | 8 6 | working | Finishing workshop |
7 | Milling and drilling machine | XZ8210C | 2 | working | Finishing workshop |
8 | CNC milling and drilling machine | TY-ZT5060 | 6 | working | Finishing workshop |
9 | OD milling machine | MB32BX500 | 2 | working | Finishing workshop |
10 | Air compressor | HLGD-75 | 1 | working | Finishing workshop |
11 | Vertical drilling machine | Z5140A | 6 | working | Finishing workshop |
12 | CNC suspended tapping machine | SKXFGS.PS | 5 | working | Finishing workshop |
13 | CNC hobbing machine | YK3180CNC3 | 6 | working | Finishing workshop |
14 | Marking machine | HZP-90*160D etc. | 6 | working | Finishing workshop |
15 | Natural gas furnace | WLS-DZ-001 etc. | 2 | working | Forging workshop |
16 | Air hammer | C41-2000 etc. | 15 | working | Forging workshop |
17 | Press | J53-2500C etc. | 18 | working | Forging workshop |
18 | Ring rolling machine | D51-450A etc. | 8 | working | Forging workshop |
19 | Electric furnace | KGPS-600KW etc. | 10 | working | Forging workshop |
20 | Compressor | 175A-20.5 etc. | 3 | working | Forging workshop |
21 | CNC sawing machine | GZ4232 | 16 | working | Raw material workshop |
22 | Automatic normalization furnace | HRDW-600KW | 8 | working | Heat treatment workshop |
23 | Suspended gas normalization furnace | WD-0138 | 2 | working | Heat treatment workshop |
24 | Shot blasting machine | Q3210,Q69 etc. | 4 | working | Finishing workshop |
Main Testing and Inspection Device
No. | Device | Type | Qty | Status | Note |
1 | End quenching machine | DZJ-I | 1 | working | Testing |
2 | Electric resistance furnace | SX2-8-12 | 2 | working | Testing |
3 | Inverted metallurgic microscope | 4XCE | 1 | working | Inspection |
4 | High temperature box resistance furnace | SX2-4-13 | 1 | working | Testing |
5 | Automatic digital display Rockwell hard-tester | 200HRS-180 | 1 | working | Inspection |
6 | Electronic Brinell hardness tester | THB-3000 | 1 | working | Inspection |
7 | HR-150B Rockwell hardness tester | HR-150B | 1 | working | Inspection |
8 | Rapid multi-element analyzer | JS-DN328 | 1 | working | Inspection |
9 | Electric arc furnace | JSDL-8 | 1 | working | Testing |
10 | Rapid multi-element analyzer(C & S) | JS-DN328 | 1 | working | Inspection |
11 | Infrared thermometer | AR872 | 2 | working | Inspection |
12 | Portable chemical composition analyzer | AR872 | 2 | working | Inspection |
13 | Test specimen sampler | KW30-6 | 1 | working | Inspection |